研究開発
NGKグループの
コア技術
独自の多彩な技術を核に、
日本ガイシは創業以来、社会の基盤を支え、
環境課題の解決に役立つ製品を開発、
提供し続けています。
競争力の源泉
必要なのは、複雑な"ジグソーパズル"を組み立てる技術
NGKグループは創立以来、古くから伝わるセラミックスの製造手法を最新の科学技術で見直し、製品ごとに最適な工程条件の組み合わせを見いだしてきました。そうした技術やノウハウの100年以上に及ぶ蓄積がNGKグループの競争力の源泉です。
セラミック製品の製造の流れ
-
- 01元になる原料の選定と「調合」
=混ぜる・練る - 02製品の形状を付与する「成形」
=形をつくる - 03製品に最適な結晶の構造を実現する「焼成」
=焼く
- 01元になる原料の選定と「調合」
-
セラミック製品の製造は硬くてもろい無機物に命を吹き込んでいく地道な作業です。
原料が製品になるまでには3段階あり、各段階で高度な技術が必要になります。
セラミックスのもとになる原料の粉末は、直径わずか1000分の1mm程度。大きいと焼成時間が長くなり、小さすぎるとひび割れやばらつきの原因となります。サイズの異なる粉末が混じるとゆがみが発生しかねません。数万種の材料から最適な原料を選び調合しなければならないのです。
調合された原料は製品の形状に応じた方法により成形され、窯で焼成されます。焼成すると原料の粉末同士がくっついて縮むため、製品に仕上がった際には、がいしで約25%、ハニセラムで約10%、サイズが収縮します。ここで重要なことは、成形の段階で粉末の間に、均一で適切な“隙間”を作っておくこと。さもないと焼成したときに縮み方がばらつき、形が変わってしまいます。窯の中の諸条件も重要です。セラミック製品の特性は、原料の粉末が固まってできた微細な結晶の構造で決まり、それは焼成するときの温度や時間、炎の色(放射温度)、雰囲気(炉内の水蒸気分圧)などに左右されます。窯の中の温度のばらつきで焼成の進み具合に差が出れば、でき上がった製品が均一になりません。
このように、各段階でさまざまな条件を満たすことで、初めて高性能なセラミック製品を作ることができます。いわば、複雑な“ジグソーパズル”。そのための技術やノウハウを幅広く蓄積していることこそが、NGKグループの競争力の源泉なのです。
私たちはNGKグループビジョン達成に向けて、この蓄積した力とDXなど最新の技術を組み合わせることにより、短期間で革新的な研究開発や技術のイノベーションを目指します。
NGKグループのコア技術
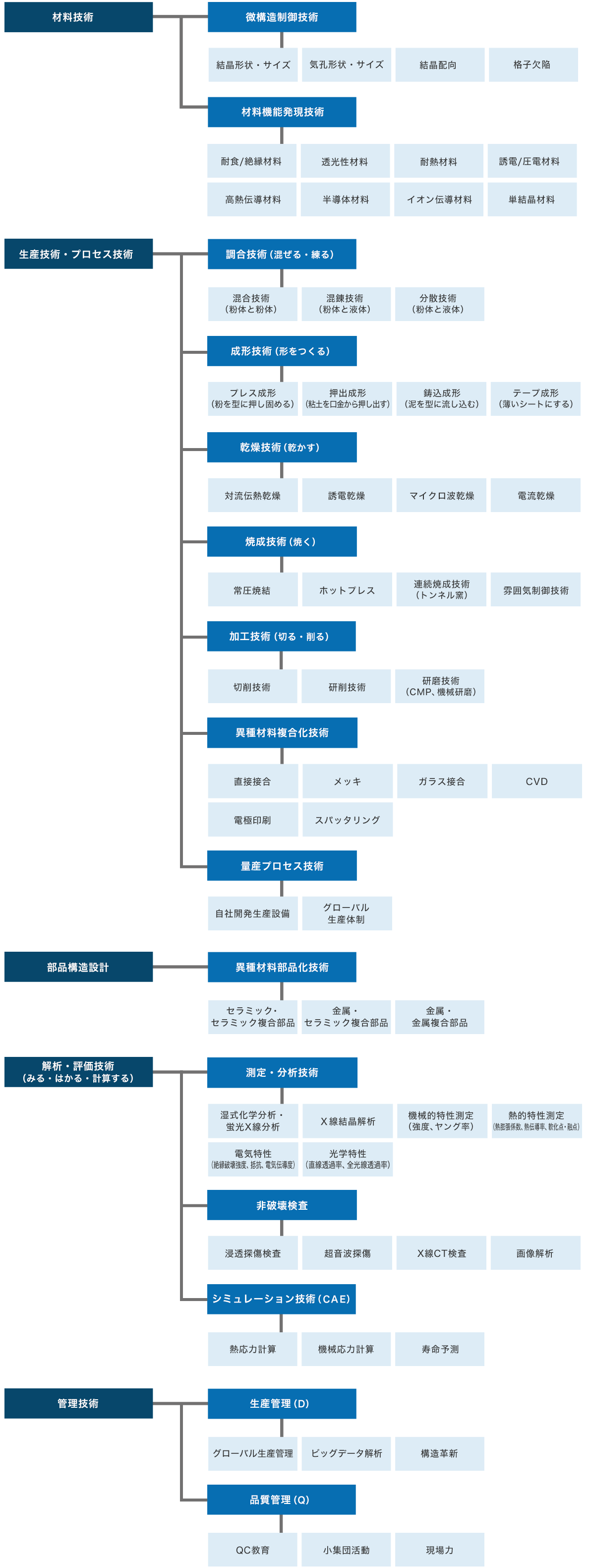